SOIL NAILING CONSTRUCTION PROCESS
Construction of works to overcome the consequences caused by slopes such as landslides, landslides are being studied and constructed in many countries. The method of using "soil nailing" technology, also known as "earth nailing", is often applied to overcome the consequences and stabilize the slope of the roof, performed on the roof surface of traffic works such as the roof of a roadway. , abutment roof of the bridge; irrigation works such as dyke roofs, dam roofs. The method of excavating the construction floor by the "top down" method has shortened the construction time and reduced the amount of excavated soil. "Earth nail" constructed according to design and technique is an effective and cost-effective method of stabilizing slopes.
1.Ground Nails Construction Preparation Work
- After surveying the construction site, the construction contractor proposes a measure that the foot, the pedestal that follows the machine will apply directly to the roof of the talus, the contractor will further process the drill rail and vertical ladder for workers to operate with. V steel (as attached method drawing), using electric winch system (or three chain hoists of 2-5 ton type) to move as well as keep the drill standing on the roof surface.
- On the top of the mechanical roof, the construction contractor uses a drill to drill into the mechanical surface with a depth of 2m -3m, maybe deeper depending on the top geology, then use steel to fix the winch (or three chain hoists 2-5 ton).
- Carrying out the construction and erection of three-phase electric winch tractors with the capacity to win heavy objects weighing 2 tons, or install a system of three chain hoists on 2 tons of the top of the talus roof for moving work. drilling machine rack and worker stand to drill holes on the taluy roof
2.Drilling Holes On Slope
Bore Positioning Work
- The ground nail hole on the roof is determined by an electronic total station and a steel ruler. The boreholes are located with an error of ±75mm, for a specified route at the entry point, the hole is drilled with an angle error of ±2.5o.
- All boreholes are systematically marked to identify the location of each hole on the construction site, using red paint to mark at the site.
- After completing the work of locating the drill holes and marking them with red paint, the construction contractor will invite the Supervision Consultant (TVGS) and supervise the Investor (Investor) or the construction contractor. The general contractor checks and accepts the location of the hole drilled in the ground.
- After locating the location of the earth nail hole, the construction contractor conducts the construction work of drilling to create the hole.
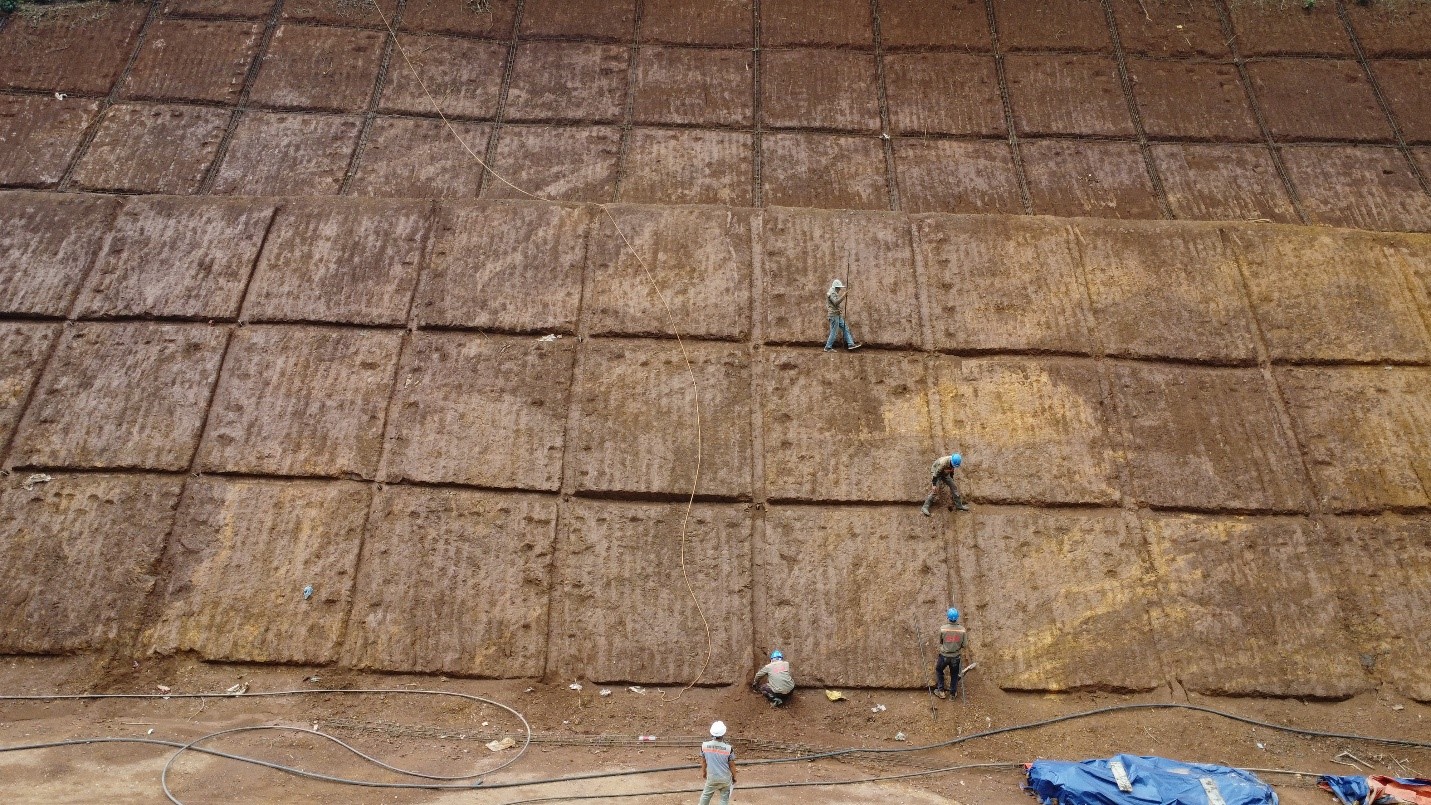
Construction Work Drilling and Creating Holes In Construction of Ground Nails
- Completing the pre-acceptance test, the construction contractor moves the drill to the position of the previously marked hole in the ground, and fixes the anchor to hold the drill.
- The construction contractor re-checks the entire drilling machine system: The certainty of the winch (chain hoist), silk cable, drill machine, worker stand. When it is certain, the construction unit invites the Investor/TVGS to check once again the entire system of drilling machines has been installed.
- After the Investor/TVGS completed the inspection of the drilling machine system and assessed it as satisfactory, the drilling and making holes commenced.
- The ground nail hole has a bore diameter of Ø110 and is drilled in sequence from the first hole of the site to the last of the site and proceeds along the roof.
- During the drilling process, there is always a technical supervision contractor on the site to ensure the quality of work and work safety on the site. In addition, technical contractors always pay attention to the air pressure of the drill. If during the drilling process there is a phenomenon of air loss (caused by encountering a strongly fractured rock area) or just losing air and collapsing the wall of the hole, stop drilling and use a specific cement grouting method such as: After: First install the tank using cement grout pressure (according to TCVN 8645-2011) so that the cement water can enter into the cracked joints and reinforce the borehole wall.
- During the drilling process, if there is a problem with the rod or blocking the hole, the Contractor will pump water into the borehole to clean it.
Protection of Ground Drilling Hole and Drainage Borehole
- If during the drilling process, the geological part outside the roof surface is weak, the construction contractor installs the anti-tube to avoid collapsing the borehole wall.
- After the hole is completed, the earth nail contractor will seal the hole to prevent debris from falling in and keep the strut in place until the work of putting the earth nail into the hole is carried out.
Borehole Acceptance Work
- The construction of ground nails, drilling to create soil nails and drainage holes has been completed, and the construction contractor will conduct internal acceptance, the entire diameter of the borehole will be checked and accepted by the meter ruler and the length of the hole. Drilling is checked and accepted with HDPE pipes marked with length, the internal acceptance process is satisfactory. The earth nail construction contractor invites the investor / TVGS unit to check and accept the hole drilled in the ground nail.
- The investor/TVGS unit conducts inspection of the borehole, after the investor/TVGS accepts the hole drilled with the ground nail, the construction contractor proceeds to change the stage of putting the earth nail into the borehole.
3.Crafting Nails
- The construction contractor will submit the detailed design of the earth nail to the investor. Immediately after the approval of the material design is obtained, the construction contractor will place and process the ground nails.
- Ground nails are made from steel, the steel used for earth nails is twisted, straight, without welds.
- The earth nail is constructed by the contractor according to the approved design.
- After being transported to the construction site, the earth nail construction contractor will process and center the ground nail.
4.Installation of Nails In Construction of Ground Nails
- All ground nails, when delivered to the construction site, will be carefully inspected and fully centered before proceeding to insert the ground nails into the borehole.
- Immediately after the acceptance of the borehole and the acceptance of the ground nail was completed (attached to the record of the acceptance of the hole and the acceptance of the ground nail material), the construction contractor carried out the insertion of the earth nail into the borehole.
- The construction of earth nails is to put the earth nails into the drill holes and is implemented by the contractor according to one of the following two options:
- Option 1: In case the construction road is favorable, the construction site on the top of the crane can work (or at the construction site with a crane available), the construction contractor will put the earth nail into the drill hole. . Before implementation, it is necessary to have an occupational safety engineer to check all equipment and materials in service of crane work such as cables, crane hooks, to ensure that all are in good working order. During construction, they must have adequate labor protection equipment. During the construction process, they must absolutely obey the deviations of occupational safety engineers and construction engineers.
- Option 2: In case the ground construction site is not suitable for the operation of the construction machine, the contractor will use all construction workers. Construction method uses a winch in combination with workers to put the anchor steel into the anchor hole, use a steel winch to the roof surface, then use a worker to guide the steel into the drilled hole and then gradually release the winch to slowly put the steel into the hole. The entire work of putting the anchor steel into the hole must be carried out by the contractor's labor safety, the investor / supervisory supervisor, the winch before construction is checked carefully, the workers participating in the construction are fully equipped with equipment. labor protection equipment, during the construction process must absolutely comply with the orders of labor safety officers.
- Immediately after the construction of the earth nail to put the earth nail into the first Zone drill hole is completed, the earth nailing contractor will invite the Investor / TVGS to inspect and take over the work.
- The Investor / Supervisory Board agrees to take over the work of putting anchor steel into the drilled hole (attached to the acceptance report signed by the representative of the Investor / TVGS) the contractor proceeds to change the phase of grouting the hole.
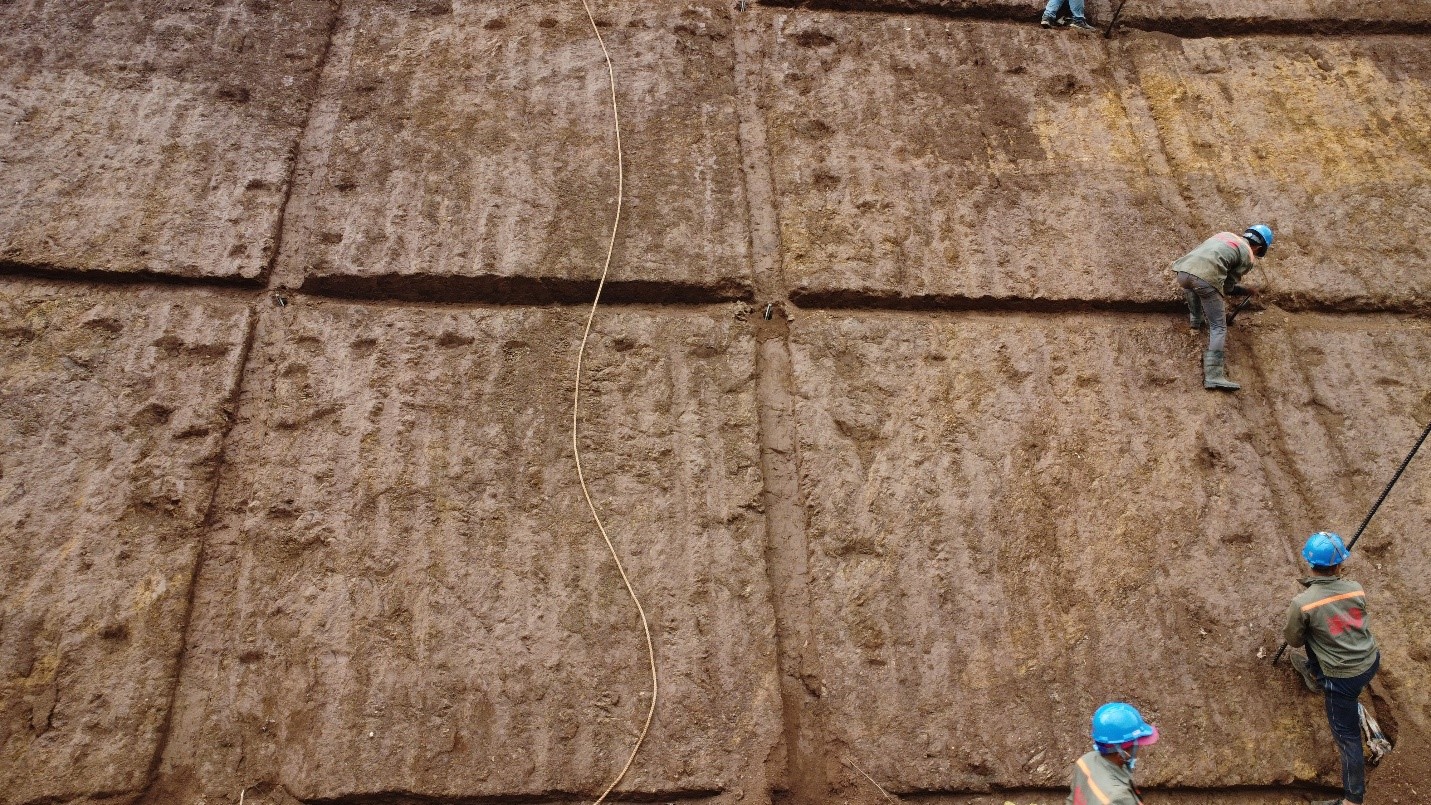
5.Mortar Pump
The purpose of the grout pump is to supply grout for the entire length of the nail. This also helps to stabilize the drilled holes. The grout also fills the void, removing any water in the hole, if any.
Materials for pump grout
- Water: Only use clean water for use
- Cement: Portlang PCB 40 . Cement
- Attached additives do not shrink, increase flexibility
Mortar pump system
Mortar Mixing System
The mixer does the work of mixing the mortar, and has a container to allow the mortar to be stirred continuously. This tank is connected to the pump located at the bottom of the double tank. The grout will be delivered to the pump. The grout is properly mixed in the barrel for about 3-4 minutes until the grout is uniform. After mixing, the mixed mortar is passed through a high-pressure pump to pump into the anchor pipe. A valve shall be fitted between the pump and the anchor inlet.
Design of mixed mortar in the construction of soil nailing
- Mortar mixes are required to be submitted and approved prior to use on site
- Before grouting, it is necessary to conduct a test on the mixed mortar
- Flow test: This is done using a conical funnel. Time taken for grout flow with a pre-measured amount of grout from 12 to 25 seconds.
- Compressive strength: a cube mortar sample of size (70x70x70) mm will be taken from the mixtures and will be tested for compressive strength after 7 days and after 28 days. Compressive strength at 7 days is not less than 27MPa and 30MPa for 28 days. Six cubes of mortar shall be taken in any batch of each working day for compressive strength testing.
Mortar pumping process
- Before grouting, the grout hose for nails is inspected and if necessary rinsed with clean water or an air compressor to remove any debris etc.
- Water, cement and additives required for grouting are kept ready.
- Cement, water and admixtures are mixed in the mixer tank in the approved proportions. This mixture will be prepared and mixed to form a homogeneous mixture. The mortar after mixing will be transferred to the pumping process.
- All grouting measures shall be taken so as to fill the grout.